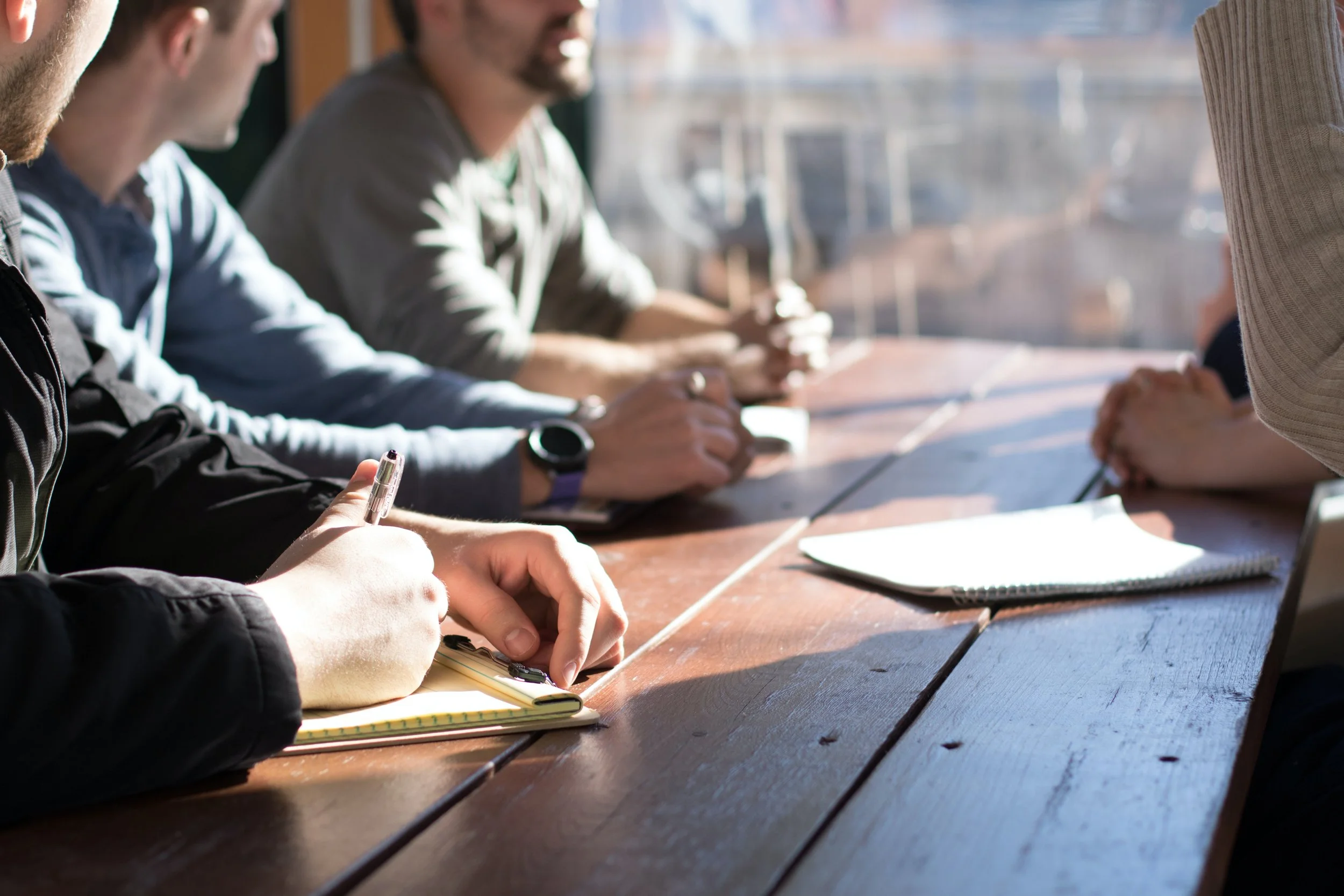
Team Building
Service Overview
At the core of this journey is the recognition that effective change starts at the top, necessitating leaders who not only desire transformation but also possess the skills to bring it about. The article outlines a three-tiered approach to Lean transformation, guiding organizations from Incremental Improvement to Systematic Improvement and culminating in Automatic Improvement, where processes seamlessly align with strategic objectives.
We introduce a proven four-phase process for successful Lean leadership, emphasizing the importance of getting ready, starting with impactful proof-of-concept pilots, achieving lasting success through expanded projects, and ultimately becoming self-sustaining. Recognizing the challenges leaders face, we position Flow Consulting as your trusted partner, bringing decades of expertise in Lean, Six Sigma, and leadership development to guide your organization through these transformative phases.
Commit to embedding Lean principles into your organizational culture, driving lasting change and operational excellence. Explore the detailed insights in our blog and let's chart a course for your Lean transformation together.
Leading a Lean Transformation
Culture change starts with the people at the top. Not only do they have to want to change, but they need to know how to change. A Lean transformation is the classic example.
A new leader comes in and recognizes the business needs far more focus on giving the customer what they want. This doesn’t mean new software, machinery or certifications, which are the solutions the existing leadership team often proposes. It means changing the way people go about their jobs, and that’s hard.
The start point for the new boss is to ensure their leadership team has the skills, knowledge and understanding to create a Lean transformation. This isn’t about training, although a lot of learning will be imparted, but about driving change through an organization.
Over the past two decades we’ve helped many clients through this transformation. They start out chaotic and internally focused and with our support they become World Class Lean organizations where improvements are automatic and cultural. Here’s how it happens.
A Journey, Not a Destination
Becoming a Lean enterprise is not about making a step change. There will be steps, but it’s more about setting the organization on an upward, continually improving, trajectory than moving to a new and slightly better status quo.
Lean is about focusing on giving the customer what they want and are willing to pay for. Anything that doesn’t contribute to this goal is wasteful, which is why we say Lean manufacturing is about driving out waste.
Lean is not about using various tools, most of which are known by their Japanese names. These will be used, but as a means to an end, and that end is the never-ending pursuit of improvement.
Three Levels of a Lean Transformation
Our experience of working with organizations that want to become Lean has led us to recognize three levels of ‘Lean-ness’. Level 1 is the beginner level, where nothing is Lean. In Level 2 there’s some recognition of what needs doing, and a degree of alignment towards the goal of becoming Lean. It’s only after attaining Level 3 though, that we can say with confidence Lean is becoming embedded in the culture.
A closer look at these three levels will help you see what’s involved in a Lean transformation. It may also give you a sense of where your organization is right now.
Level 1: Incremental Improvement
Here the organization is in a reactive, opportunistic mode. Improvement activities are initiated in response to a problem or because someone has seen a way of improving a process step or activity. They may yield some lasting improvement, or just as likely, they push the problem somewhere else because root causes weren’t properly identified and addressed.
At this level we observe:
When improvement programs exist they focus on skills training, with employees being free to use these tools as they see fit
Minimal linkage to the critical strategic imperatives of the organization, as leaders aren’t converting strategy into measurable improvements
Level 2: Systematic Improvement
Here leaders are attempting to provide strategic direction to improvement efforts. It’s understood that the organization must be proactive in identifying opportunities, and these should be prioritized in alignment with the overall strategy.
In general, with organizations at this level, we observe:
Recognition of the need for a systematic, structured, repeatable approach to improvement
All key processes are included and priorities are established
A range of quality and lean tools are deployed in an appropriate sequence
The resulting improvement efforts are linked to the strategy developed by the top leadership team
Level 3: Automatic Improvement
An organization at Level 3 is truly Lean. There’s a strong process focus and tight alignment between strategy and improvement efforts. Measurement is a way of life, so team members can see how things are going and where improvement is needed.
A wide range of Lean and quality tools are deployed to find and make improvements. This happens naturally as the expertise and knowledge for their use is deeply embedded in the organization, and the DMAIC (Define, Measure, Analyze, Improve and Control) approach is applied consistently.
At this level we observe:
Processes are optimized, measurable, and adjustable when data warrants
Clear ownership by change experts that ensures automatic diagnosis and improvement
Very tight linkage to the organization strategy so improvements tie directly to the desired goals and measurements
Moving Through The Levels
To make a Lean transformation is to move from Level 1 to Level 3. The role of the leadership team is to bring about that change, and the job of the person in overall charge is to help the team do just that.
This is where problems set in. Unless the person in charge has expertise in team development, quality improvement and Lean tools, and unless they’re blessed with plenty of time, (most unlikely), they will need help.
Flow Consulting can be that resource. We’ve developed and proven a unique four-phase process for leading a Lean transformation. These phases are:
Phase 1, Getting Ready
Phase 2, Getting Started
Phase 3, Achieving Lasting Success
Phase 4, Becoming Self-Sustaining
Here’s a look at what’s involved with each phase.
Phase 1: Getting Ready
This is about creating alignment, otherwise known as getting everyone “on the same page”. It entails ensuring the team agrees on the problem to be addressed and that there’s a strategy for where the organization needs to go.
We promote a data-driven approach focusing on the ‘critical few’ issues rather than the ‘trivial many’. This is done with the help of the Baseline and Hoshin Kanri (or “Policy Deployment”) tools.
Baseline is a fact-based problem-solving process used for setting priorities and taking action. It works by creating ‘common knowledge’ and the organizational motivation to overcome inertia and get something done.
Hoshin Kanri is a method of ensuring plans and actions are driven by the strategic goals of the organization. Typically, it entails setting goals, (no more than five), and establishing KPIs to measure progress on each one. Once done, actions are identified and taken in pursuit of the goals and as measured by the KPIs.
Only when the leadership team has agreed on what needs doing and why, plus how it will be done, is the organization ready to actually start working towards the Lean transformation.
Phase 2: Getting Started
In many organizations there’s inertia and even skepticism about new ‘initiatives’. Many people prefer to sit back and watch before deciding to get on board with the changes, and this is a problem that must be overcome.
Our approach is to run a ‘Proof-of-Concept’ pilot. This uses the output of the Baseline and Hoshin Kanri exercises to build a foundation of belief that generates forward momentum.
The way this works is to:
Select a limited number of significant projects
Hand pick the people for these projects, preferably those favorably inclined towards change and improvement, to form a ‘coalition of the willing’
Provide action-based education in techniques like Lean Six Sigma, paired with strong leadership and coaching, to ensure the teams get something done
Add strong communication and attention from the leadership team to reinforce the importance of this effort
It’s important this is not a long, drawn out process. We’ve found that keeping the timescale tight and maintaining a dual focus on Lean Education and Process and Change Leadership significantly enhances the level of success achieved.
Phase 3: Achieving Lasting Success
An early ‘win’ in Phase 2 helps drive out initial skepticism and provides a solid basis for rolling the transformation out across the organization. More people will be interested in getting involved and there will be less resistance to making changes and suggesting and trying new ideas.
Highlights of Phase 3 include:
Larger projects that will have great impact are undertaken
More people are trained in Lean techniques, and those early ‘converts to the cause’ receive additional training to deepen their understanding and ability to lead
Education begins to move in-house as the early ‘converts’ become able to share their knowledge and experience
The sense of working towards a common set of goals improves leadership and communication
There’s greater focus on the ‘critical few’ issues identified during Phase 1 so resources aren’t diluted chasing ‘trivial many’ problems
Change leaders visibly apply the DMAIC method, acting on strategies and goals, measuring results and adapting behaviors for greater gain
Phase 4: Becoming Self-Sustaining
Phase 3 has instilled a focus on process rather than project, with alignment understood and accepted throughout the organization. Everyone knows why changes are needed, they understand how changes will be made, and they are committed to making the changes work.
This is where Phase 3 transitions into Phase 4, where the new tools, methods and ideas are no longer new but just ‘the way we do things’. This doesn’t happen by chance, and once achieved it’s critical to prevent any backsliding to the old ways of working.
Now armed with Leadership, Alignment, Education and measurable success, the key is to sustain and enhance all that has gone before. Core elements of this are:
Continue bringing education and training in house (the trainees become the trainers)
Move successful early disciples into key leadership positions (so they can ‘walk the talk’ to reinforce the expected behaviors)
Measure, measure, measure – so you know what impact this is having on the operations
Develop or purchase a standard set of materials
Expand and refine governance
Expand the coalition, make cross-business connections
Keep communicating what is being done, why it’s being done, and how it’s going, widely and often
A Partner for Your Lean Transformation
Once an organizational culture has become established it’s extraordinarily difficult to change. Unfortunately though, the wrong culture, meaning one that doesn’t follow Lean principles, doesn’t provide a strong platform for growth and may be actively harming the prospects for the organization.
We’ve encountered many such cases where the leader, and often the leadership team, want to bring about a Lean transformation but they don’t know where to start, and quite possibly lack the skills and experience.
This is where Flow Consulting can help. With decades of experience in Lean, Six Sigma and leadership development, we bring the expertise needed. Working with senior leadership, we’ll develop a plan, guide and coach the personnel, and deliver the training needed to bring about your Lean transformation. It won’t be easy but it will bring about a customer-focused Lean culture.