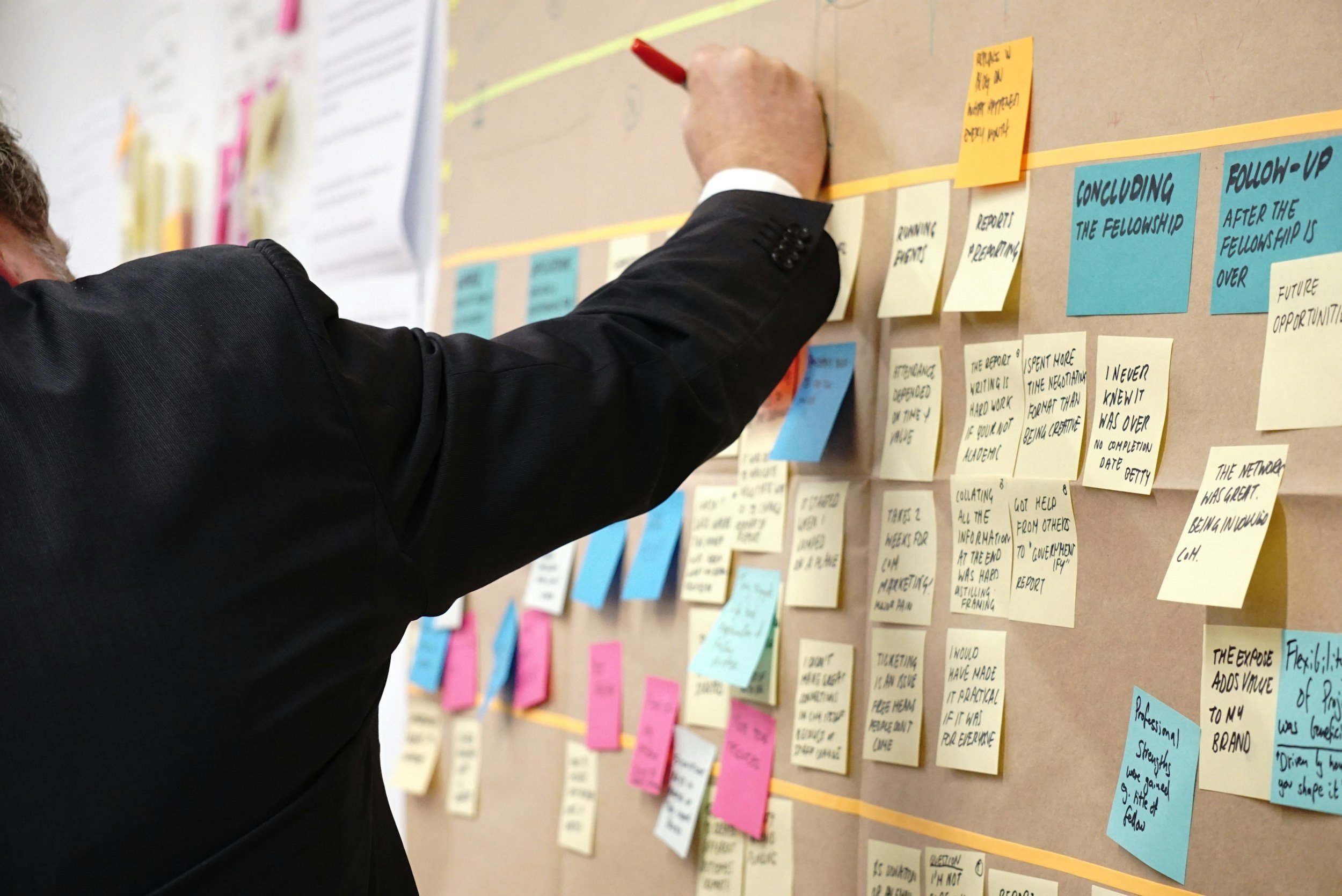
Visual Management
Service Overview
Are you convinced that your Operations Team is far from world class? Are they delivering exactly what the customer wants exactly when the customer wants the product to be delivered – at maximum efficiency? As a business leader you want to use the latest combination of Lean and Six Sigma tools and principles to move your Operations Team towards world class lean operations. Combining Lean and Six Sigma offers an advantage in improving organizational capability and sustainable improvement.
Lean
Simply put, Lean means creating greater customer value with fewer resources. Lean leaders know how to create an environment that engages their people in continuous process improvement. Lean provides the platform and core principles – focus on specifying value from the eye of the customer, identifying the value stream and eliminating waste, making value flow at the pull of the customer, involving and empowering employees, and continuously pursuing perfection.
Six Sigma
Six Sigma is a disciplined, data-driven methodology for eliminating product, process and service defects in any process – from manufacturing processes to transactional services. The Six Sigma DMAIC approach is a great way to organize many projects – Define, Measure, Analyze, Improve, Control. Six Sigma focuses on relentless pursuit of variation reduction, measured based on standard deviation, bench marked on sigma level and defect per million opportunities, using proven problem solving tools.
Lean means creating more customer value with fewer resources. A lean thinking leader understands customer value and fostering an environment where the organization continuously strives to improve. Operations transformation towards world class performance results in shorter cycle time, lower inventory, higher quality, and more satisfied customers.
When faced with improving an organization’s performance, Lean thinkers ask a few critical questions:
What value do we provide; what customer problems do we solve? What is our ‘True North’?
How do we improve the work we do?
How do we build and grow the organizational capability?
What leadership behaviors and management systems are needed to support the new way of working?
What assumptions, values, principles drive the culture change? Why change?
Organizational transformation is about planning, deploying, and measuring organization-wide strategies for value creation by disciplined business process improvement. Many organizations find the combination of Lean, Six Sigma, and Organization Development methodologies to be especially effective.
There are lots lean operations transformation road maps and recipes. To start, pick and adopt a proven and robust strategic deployment framework. The dimensions should include essentials as:
Leadership and Planning – vision, principles, plans, behavior
Value Stream Improvement – mapping, improvement ideas, kaizen
Workforce Engagement – everyone every day trying to get better
Improvement Methodology – tools and techniques, structured methods
Monitoring and Sustaining – communications, knowledge management, sharing
Facility Layout
Facilities are expensive, and can exist for decades. Facility Layout and Planning can be an important competitive advantage. A properly designed facility can:
Operate at low cost
Flexibly accommodate frequent new products and services
Produce high mix of products
Produce high and low volume
Produce at very high quality level
Design new facilities or transforming existing facilities to be world class can be a challenge. Maximizing speed and employee effectiveness while minimizing cycle times and product movement means having the right greenfield facility layout.
Four facility layout principles:
Flow – smallest batch possible moving through the process without stopping
Takt – at the drum beat of the customer
Pull – making only what is needed, when it is needed
Zero Defects – with reliable, repeatable execution
Steps to take:
Plan – collect information and document assumptions
Analyze product and process operations
Determine capacity requirements – number of work areas or machines, and floor space required
Determine materials flow
Determine layout alternatives
Do – sketches, table top models, simulations, implementation
Check – throughput, capacity, work-in-process
Act – adjust
Transforming Existing Operations
Where does the new equipment or business function go? Often where ever there’s available space. Over time our facilities and processes get fragmented and disconnected. The physical and social ‘spaghetti’ that is created when businesses evolve will often break the flow of goods and information. This is a waste.
Sometimes we are forced to free up space, rarely do we have the capability to continually reconfigure our available space.
Mistakes to avoid:
Jumping in to a new facility layout design without having a design process.
Expecting a perfect design before implementation. Near perfect might be achievable, but at the cost of longer design time and delayed implementation. Countermeasure: get to 80% and then apply continuous improvement.
Bigger isn’t better. Design the equipment and facilities to meet the expected demand rate or takt time, rather than designing the fastest or largest possible.