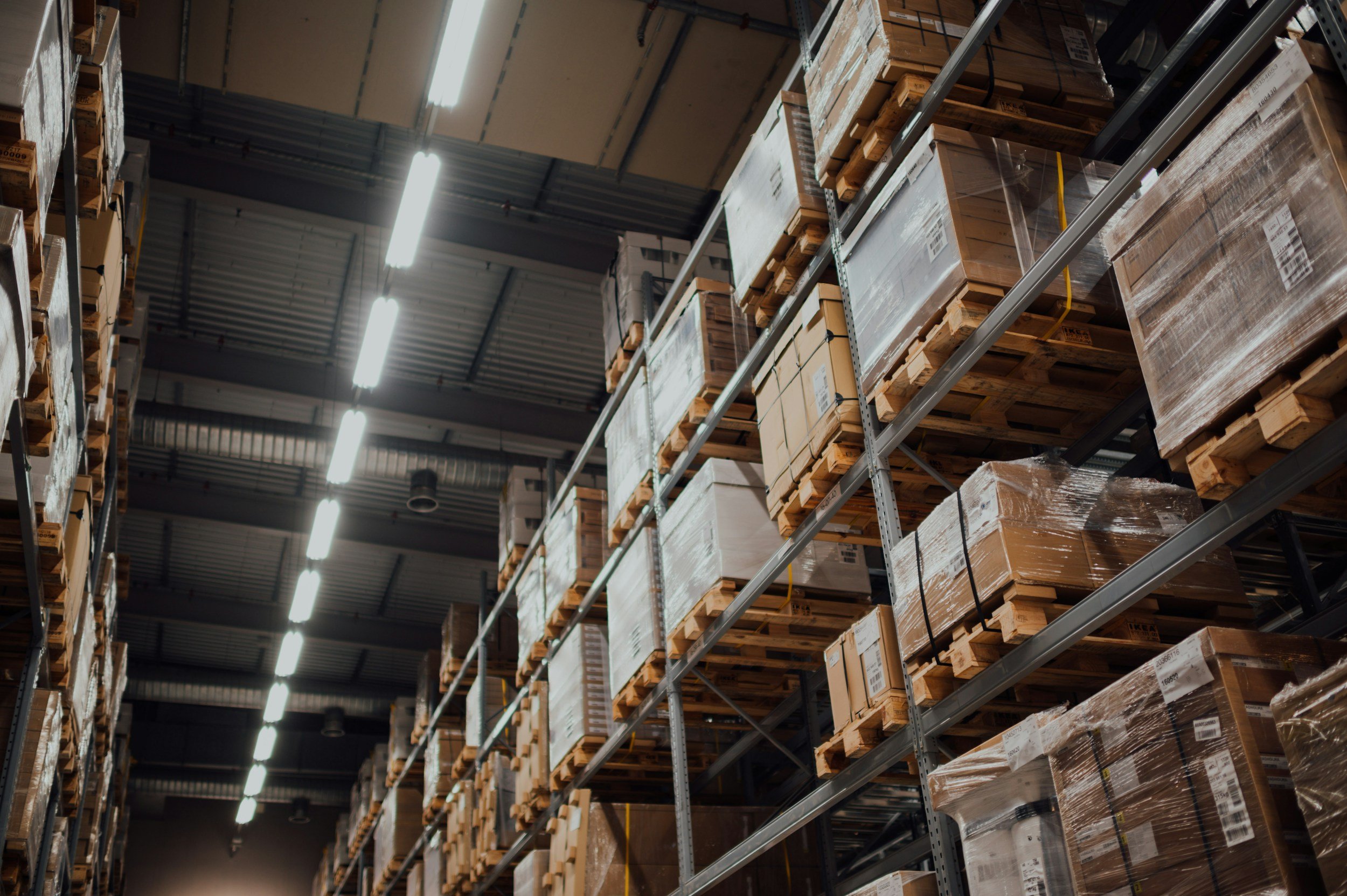
Warehouse Optimization
Service Overview
Warehouse and logistics are at the heart of any successful lean supply chain. Warehouse space optimization and product slotting optimizes all aspects of your warehouse and logistics; whether it’s facility layout, inventory analysis, or operational excellence you can bring Lean thinking to your warehouse and logistics operations.
Warehouse Space Optimization
Are you sure you have the right warehouse space, with warehouses in the right locations?
Are you optimizing inventory storage costs within your business?
Here are tools your team should be using to minimize working capital and operating expense costs of warehousing while optimizing the delivery service to your clients:
ABC Analysis
Warehouse Layout & Storage Types
Facility Layout (AutoCAD)
Pick Modules and Racking design, selection, installation
Slotting (right product in the right place)
Simulation & optimization with Slot 3D
Dock operations
Labor productivity: waves and order queue
Pick Technologies – pick to light
Warehouse Slotting – Inventory Profiling
Warehouse Product Slotting is defined as the intelligent location of product in a warehouse or distribution center for the purpose of optimizing material handling efficiency. Sometimes called inventory slotting, or profiling, it identifies the most efficient placement for each item in a distribution center or warehouse. Since each instance is unique, product slotting depends on a variety of factors.
Benefits from good warehouse slotting include:
Picking Productivity
Travel time can often account for up to 60% of a picker’s daily activity. A good product slotting strategy can reduce travel time thereby reducing picking labor.
Efficient Replenishment
By sizing the pick face locations based upon a standard unit of measure (case, pallet) for the product in question you can significantly reduce the labor required to replenish the location.
Work Balancing
By balancing activity across multiple pick zones you reduce congestion in the zones, improve material flow and reduce the total response time for a given order or batch of orders.
Load Building
To minimize product damage, heavy products are located at the beginning of the pick path ahead of crushable product. Product may also be located based on case size to facilitate pallet building.
Accuracy
Similar products are separated to minimize the opportunity for picking errors.
Ergonomics
High velocity products are placed in a “golden zone” to reduce bending and reaching activity. Heavy or oversized items are placed on lower levels in the pick zone or placed in a separate zone where material handling equipment can be utilized.
Pre-Consolidation
By storing and picking product by family group you may be able reduce downstream sorting and consolidation activity. This is particularly important in a retail environment to facilitate efficient restocking at the stores.
The Importance of Ongoing Slotting Maintenance
Operations managers typically do a good job of slotting their warehouse initially. Over time, however, customer demand changes, products come and go, and before too long labor costs are way up, order fulfillment rates are way down and response times are negatively impacting customer service and profitability. It is important to continually re-slot the warehouse to keep it operating at maximum efficiency. Some clients re-slot their highest movers (typically also their most profitable products) on a daily or weekly basis.